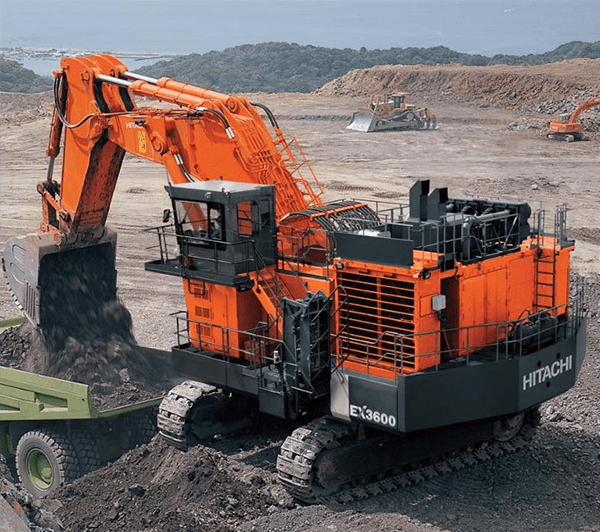
Figure 1: Hitachi excavator.
Mining wear parts are critical components of mining equipment that are designed to withstand the harsh and abrasive conditions of mining operations. However, even the most durable wear parts will eventually wear out and need to be replaced.
In this article, we will discuss some tips for prolonging the lifespan of mining wear parts.
1. Tips for Prolonging the Lifespan of Mining Wear Parts
By following these tips, mining companies can prolong the lifespan of their wear parts and reduce downtime.
1.1 Material Selection
One of the most critical factors in ensuring the longevity of mining wear parts is the selection of appropriate materials. The material used for the wear part should be able to withstand the harsh mining environment and resist abrasion, impact, and corrosion.
Some common materials used for mining wear parts include high-chrome white iron, steel, and rubber. Each material has its advantages and disadvantages, and the choice depends on the specific application and conditions. Therefore, it is essential to consult with experts and choose the right material for each wear part.

Figure 2: High manganese steel alloy.
1.2 Regular Maintenance
Another essential factor in prolonging the lifespan of mining wear parts is regular maintenance. Regular inspection, cleaning, and repair can prevent minor issues from becoming major problems and reduce downtime. Maintenance activities should be performed according to the manufacturer's recommendations and based on the equipment usage and condition.
For example, liners may need to be inspected and replaced more frequently if the equipment is used in a high-abrasion environment. By conducting regular maintenance, operators can ensure that the equipment operates at peak efficiency and avoid costly repairs and replacements.
1.3 Correct Installation
Proper installation is crucial for the longevity of mining wear parts. Incorrect installation can cause premature wear, misalignment, and other issues that can shorten the lifespan of the wear part and affect the equipment's performance.
Therefore, it is important to follow the manufacturer's installation instructions carefully and ensure that the wear part is installed correctly. This includes using the right tools, torque settings, and alignment procedures.
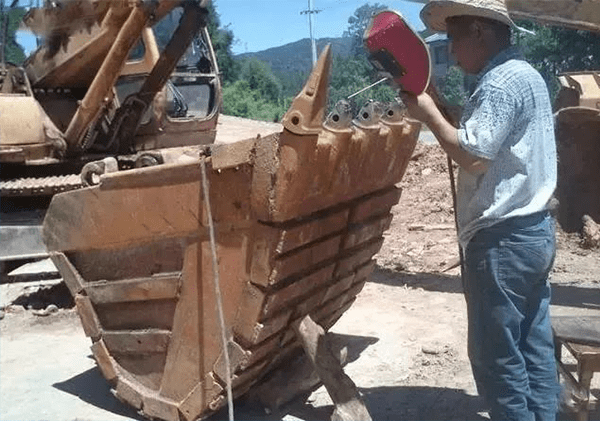
Figure 3: Install bucket teeth for an excavator bucket.
1.4 Lubrication
Proper lubrication is another critical factor in prolonging the lifespan of mining wear parts. Lubrication helps to reduce friction, prevent wear, and extend the life of the wear part. However, too much or too little lubrication can be harmful to the equipment.
Therefore, it is important to follow the manufacturer's lubrication recommendations and use the appropriate lubricant for each application. Operators should also monitor the lubrication system regularly and ensure that it is functioning correctly.
1.5 Performance Monitoring
Monitoring the performance of mining wear parts is essential for detecting issues early and preventing catastrophic failures. Performance monitoring involves measuring the wear rate, tracking the performance indicators, and comparing the data with the manufacturer's specifications.
By monitoring the performance of the wear parts, operators can identify potential problems before they cause significant damage and take corrective action. This can help to avoid costly repairs and downtime and ensure that the equipment operates at optimal efficiency.
1.6 Proper Storage
Proper storage of mining wear parts is critical for maintaining their performance and lifespan. Wear parts should be stored in a dry, clean, and protected environment. Exposure to moisture, dirt, and other contaminants can cause wear and tear on mining wear parts, reducing their efficiency and lifespan.
When storing wear parts, they should be kept in their original packaging or in a container that is suitable for their size and shape. Wear parts should also be stored in a way that prevents them from touching each other, as this can cause damage to their surfaces.
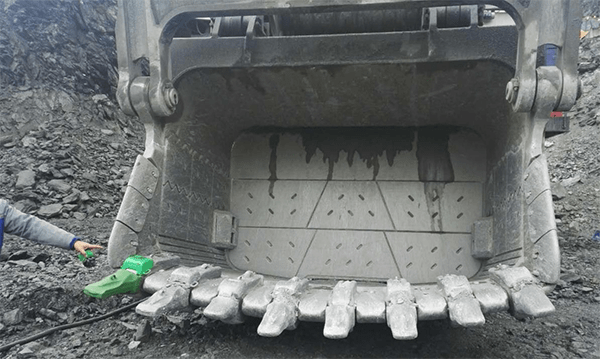
Figure 4: A&S custom excavator bucket teeth in green.
1.7 Replacement and Upgrades
Despite regular maintenance, mining wear parts will eventually wear out and need to be replaced. It is essential to monitor the wear and tear of wear parts and replace them before they fail. Failing to replace worn-out wear parts can lead to equipment failure and downtime, which can be costly for mining operations.
Upgrading mining wear parts can also help improve their performance and lifespan. Newer wear parts are often made from more durable materials and have improved designs, which can increase their efficiency and lifespan. Upgrading wear parts can be a cost-effective way to improve the efficiency and productivity of mining operations.
1.8 Training and Education
Proper training and education of mining equipment operators and maintenance personnel is critical for ensuring the efficiency and lifespan of mining wear parts. Operators and maintenance personnel should be trained on the proper use, maintenance, and replacement of wear parts.
Operators should be trained on how to properly operate equipment to prevent unnecessary wear and tear on wear parts. Maintenance personnel should be trained on how to properly inspect, clean, lubricate, and replace wear parts. Proper training and education can help prevent unnecessary damage to wear parts, prolonging their lifespan.
1.9 Collaboration with Manufacturers and Suppliers
Collaboration with wear parts manufacturers and suppliers can also help prolong the lifespan of mining wear parts. Manufacturers and suppliers can provide guidance on the proper use, maintenance, and replacement of wear parts. They can also provide recommendations for upgrading wear parts to improve their performance and lifespan.
Collaboration with manufacturers and suppliers can also help mining companies stay up-to-date on the latest advancements in wear part technology. This can help them make informed decisions on when to upgrade their wear parts to improve the efficiency and productivity of their mining operations.
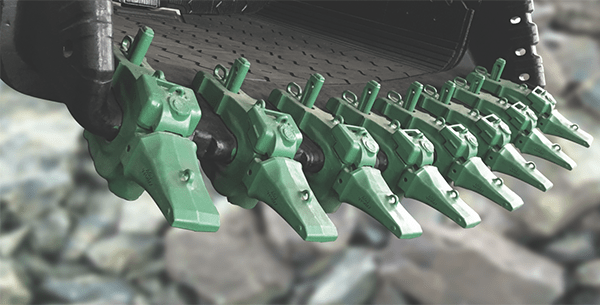
Figure 5: Brand new bucket teeth.
2. How Long Do Mining Wear Parts Typically Last and When Should They be Replaced?
The lifespan of mining wear parts can vary depending on several factors such as the type of equipment, the conditions in which they are used, the type of material being processed, and the maintenance practices followed. However, some general guidelines can help determine when to replace these parts.
For example, excavator bucket teeth can last anywhere from 500 to 3000 hours depending on the severity of the application and the quality of the tooth. Similarly, conveyor belts can last between 1 to 5 years depending on usage, environment, and maintenance. Crusher liners may need to be replaced every 6 to 12 months depending on the abrasive nature of the material being processed.
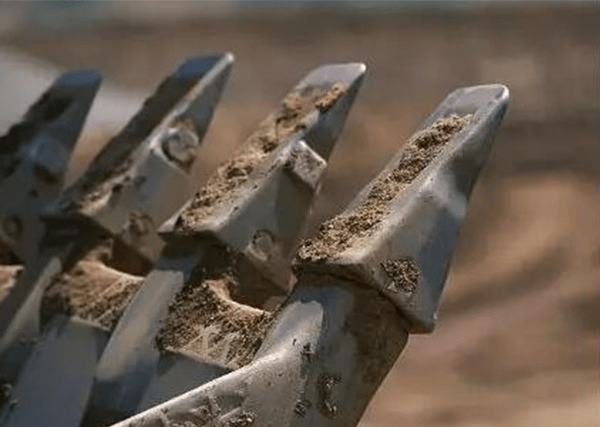
Figure 6: Excavator bucket teeth.
It is important to regularly inspect mining wear parts for signs of wear or damage and replace them before they become a safety hazard or cause significant downtime. Worn-out parts can lead to reduced efficiency, increased energy consumption, and higher maintenance costs.
Therefore, it is recommended to follow the manufacturer's recommendations for maintenance and replacement intervals and keep accurate records of the parts' usage and condition.