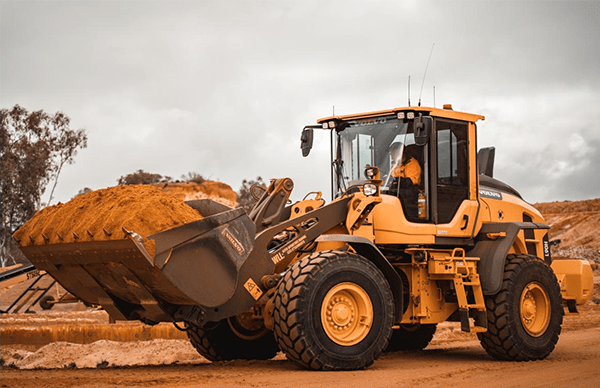
Figure 1: Loader.
Mining is a complex and demanding industry that requires a lot of heavy machinery, equipment, and tools. All these elements work together to extract minerals and other valuable resources from the earth.
However, mining equipment is subject to wear and tear, which can decrease their performance and increase downtime. As a crucial component of mining equipment, wear parts are can help protect the equipment from damage and ensure that it continues to function effectively. In this article, we will discuss the common types of mining wear parts and their functions.
1. Introduction to Mining Wear Parts
Mining wear parts are components that are designed to withstand the harsh and abrasive conditions of mining. These parts are made from high-strength materials that can withstand the wear and tear caused by the abrasive nature of the materials being mined. Mining wear parts are critical for maintaining the efficiency, productivity, and safety of mining operations.
2. Types of Mining Wear Parts
There is a wide range of mining wear parts available, each designed for a specific purpose. Here are some of the common types of mining wear parts:
2.1 Crusher Wear Parts
Crushers are used to break down large rocks, minerals, and other materials into smaller, more manageable pieces. Crusher wear parts include jaw plates, cone liners, bowl liners, mantles, and impact bars.
These parts are made from high-strength materials such as manganese steel and can withstand the abrasive nature of the materials being crushed. Crusher wear parts are critical for maintaining the performance and efficiency of crushers.
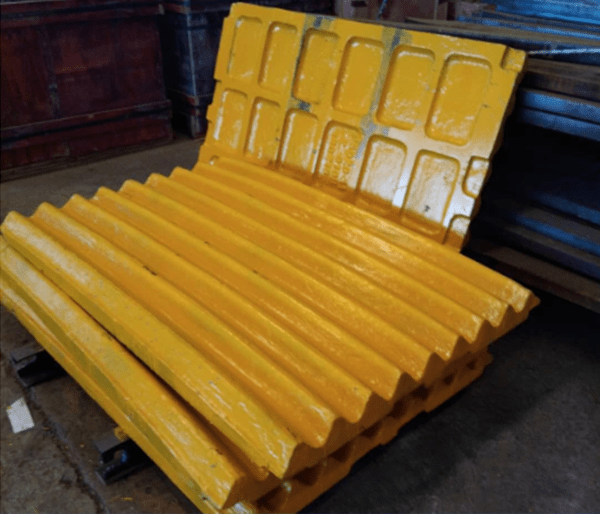
Figure 2: Crusher jaw plate.
2.2 Grinding Mill Wear Parts
Grinding mills are used to grind minerals and other materials into fine particles. These mills rely on wear-resistant liners and grinding media to perform their function. Grinding mill wear parts include liners, grinding balls, and grinding rods.
These parts are made from materials such as steel, rubber, and ceramic, which are highly resistant to wear and tear. Grinding mill wear parts are critical for maintaining the efficiency and productivity of grinding mills.
2.3 Excavator and Loader Wear Parts
Excavators and loaders are used to move large volumes of earth and minerals. These machines rely on wear-resistant components such as bucket teeth, cutting edges, and adapters to perform their function.
Excavator and loader wear parts are made from materials such as cast steel and carbide, which are highly durable and resistant to wear and tear. These parts are critical for maintaining the performance and productivity of excavators and loaders.
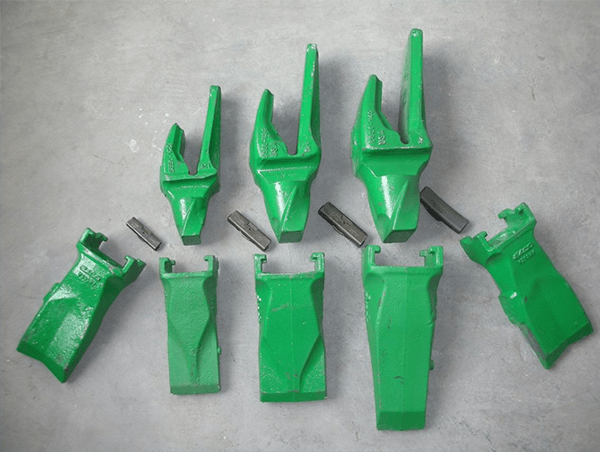
Figure 3: Loader bucket tooth.
2.4 Conveyor Wear Parts
Conveyors are used to transport minerals and other materials from one point to another within a mine. Conveyor wear parts include idlers, rollers, and belts.
These parts are made from materials such as steel and rubber, which are highly resistant to wear and tear. Conveyor wear parts are critical for maintaining the efficiency and productivity of conveyors.
2.5 Drilling Wear Parts
Drilling is an essential process in mining, used to extract minerals and other resources from the earth. Drilling wear parts include drill bits, drill rods, and drilling fluids.
These parts are made from materials such as tungsten carbide, steel, and diamond, which are highly resistant to wear and tear caused by drilling. Drilling wear parts are critical for maintaining the efficiency and productivity of drilling rigs.
2.6 Hydraulic Hoses
Hydraulic hoses are used to transmit hydraulic fluid from one part of a machine to another. They are subject to high levels of wear and tear due to the pressure and temperature changes that occur within the hydraulic system. As a result, hydraulic hoses must be replaced regularly to ensure the continued safe and efficient operation of the machine.
There are several types of hydraulic hoses available, including braided hoses, spiral hoses, and multi-spiral hoses. Braided hoses are the most commonly used type of hydraulic hose and are suitable for most applications. Spiral hoses are used for high-pressure applications, while multi-spiral hoses are used for extremely high-pressure applications.
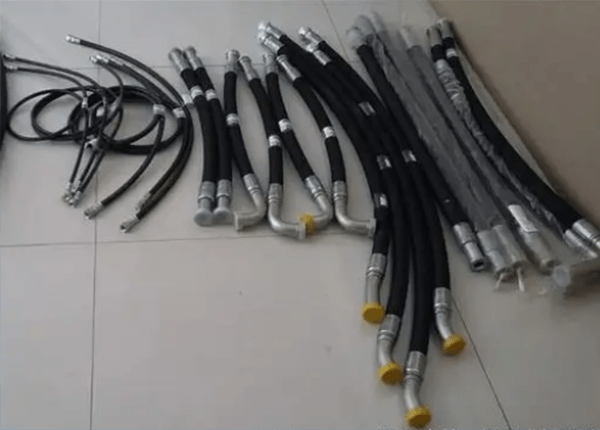
Figure 4: Hydraulic hoses.
3. Functions of Mining Wear Parts
Mining wear parts play a critical role in maintaining the efficiency, productivity, and safety of mining operations. Here are some of the functions of mining wear parts:
3.1 Protecting Equipment
Mining wear parts protect equipment from the abrasive nature of the materials being mined. These parts act as a barrier between the equipment and the materials being processed, preventing damage and wear and tear to the equipment.
3.2 Improving Efficiency and Productivity
Mining wear parts can improve the efficiency and productivity of mining operations by ensuring that equipment is always operating at optimal levels. When mining wear parts are worn out or damaged, they can decrease the efficiency and productivity of mining operations.
3.3 Reducing Downtime
Mining wear parts can reduce downtime by ensuring that equipment is always operating at optimal levels. When mining wear parts are worn out or damaged, they can lead to equipment failure, which can result in downtime. By using high-quality mining wear parts, mining companies can reduce downtime and increase productivity.
3.4 Enhancing Safety
Mining wear parts can enhance safety by ensuring that equipment is operating at optimal levels. When mining wear parts are worn out or damaged, they can lead to equipment failure, which can increase the risk of accidents and injuries. By using high-quality mining wear parts, mining companies can enhance safety and reduce the risk of accidents and injuries.
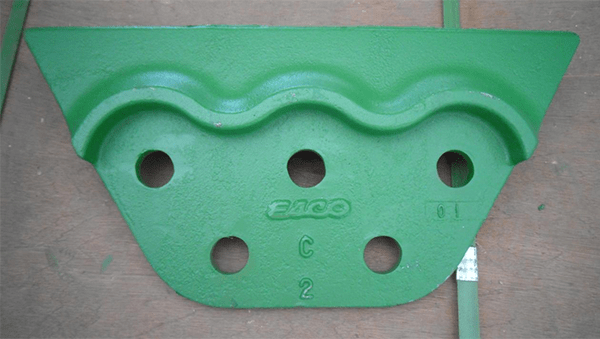
Figure 5: Side cutter.
4. Choosing the Right Mining Wear Parts
Choosing the right mining wear parts is critical for ensuring the efficiency, productivity, and safety of mining operations. Here are some factors to consider when choosing mining wear parts:
4.1 Material
The material used to make mining wear parts is critical for their durability and resistance to wear and tear. Different materials are suitable for different applications, and choosing the right material can significantly improve the performance and lifespan of mining wear parts.
4.2 Design
The design of mining wear parts is critical for ensuring their functionality and compatibility with equipment. Different mining wear parts have different designs, and choosing the right design can significantly improve the efficiency and productivity of mining operations.
4.3 Quality
The quality of mining wear parts is critical for their durability and resistance to wear and tear. High-quality mining wear parts are made from high-strength materials and have precise designs, ensuring optimal performance and long service life.
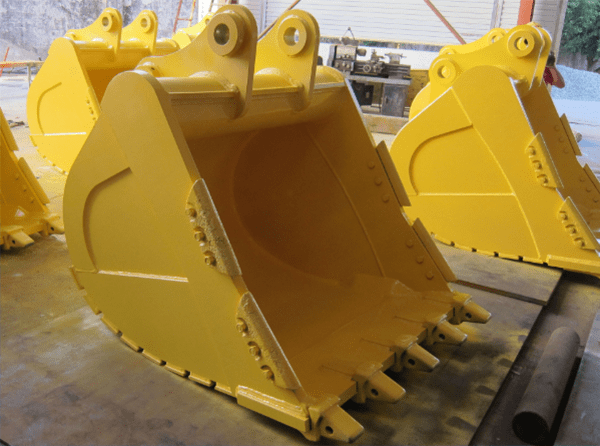
Figure 6: Excavator buckets.
5. Conclusion
Mining wear parts are critical components of mining equipment that are designed to withstand the harsh and abrasive conditions of mining operations. There are many types of mining wear parts available, each with a specific function and made from high-strength materials that can withstand wear and tear.
Choosing the right mining wear parts is critical for ensuring the efficiency, productivity, and safety of mining operations. By using high-quality mining wear parts, mining companies can reduce downtime, increase productivity, and enhance safety.