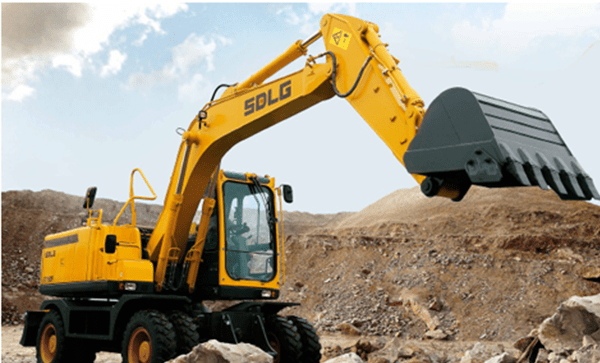
Figure 1: SDLG excavator.
Mining wear parts are essential components in the mining industry that enable equipment to withstand extreme operating conditions. These parts are designed to endure heavy abrasion, impact, and corrosion, which are common in mining operations.
The choice of materials used to manufacture these wear parts is crucial since it determines their durability and performance. In this article, we will explore the common materials used to manufacture mining wear parts and their properties.
1. Introduction to Mining Wear Parts
Mining wear parts are components of mining equipment that are designed to withstand the harsh conditions and abrasive environments present in mining operations. These parts include buckets, teeth, blades, shovels, hammers, and crushers, among others.
These parts are subjected to high levels of wear and tear due to the abrasive nature of the materials being extracted. As a result, the materials used to manufacture these components must be able to withstand the extreme conditions and provide long-lasting performance.
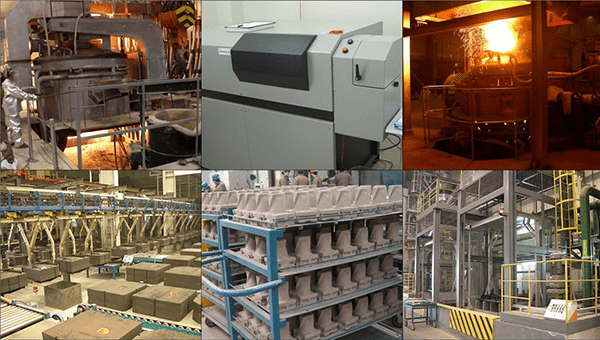
Figure 2: Mining wear parts production equipment.
2. Common Materials Used in Mining Wear Parts
There are several materials commonly used in the manufacture of mining wear parts. These materials vary in their properties and are selected based on the specific application and requirements of the component being manufactured. Some of the most commonly used materials in mining wear parts include:
2.1 Manganese Steel
Manganese steel is a high-strength material that is often used in the manufacture of mining wear parts. This material is known for its excellent toughness and wear resistance, as well as its ability to work-harden under impact and abrasion.
Manganese steel is commonly used in the manufacture of crusher liners, ball mill liners, and shredder wear parts. It is also used in the construction of heavy-duty machinery such as excavators and bulldozers.
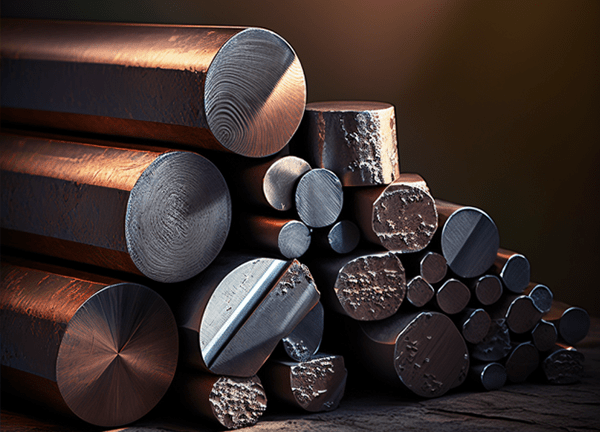
Figure 3: High manganese steel.
2.2 High Chrome Iron
High chrome iron is another commonly used material in the manufacture of mining wear parts. This material is known for its high resistance to wear and corrosion, making it ideal for use in harsh environments.
High chrome iron is often used in the manufacture of grinding balls, shredder hammers, and impact crusher blow bars. It is also used in the construction of heavy-duty machinery such as dragline buckets and excavator teeth.
2.3 Tungsten Carbide
Tungsten carbide is a hard and dense material that is known for its high resistance to wear and abrasion. This material is often used in the manufacture of wear parts that are subjected to extreme wear and tear.
Tungsten carbide is commonly used in the manufacture of drill bits, cutting tools, and wear plates. It is also used in the construction of heavy-duty machinery such as drill rigs and tunnel boring machines.
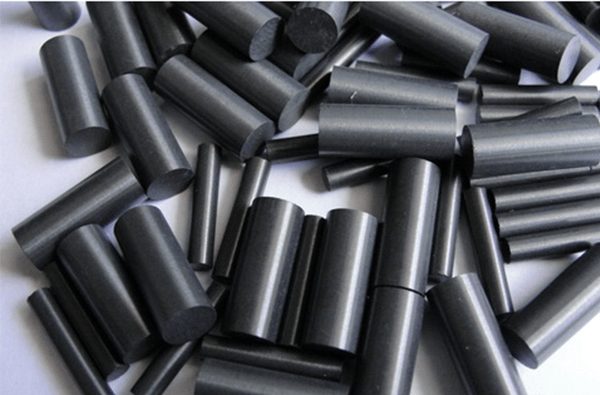
Figure 4: Tungsten carbide.
2.4 Ceramic
Ceramic is a material that is known for its high resistance to wear and corrosion. This material is often used in the manufacture of wear parts that are subjected to harsh chemical environments.
Ceramic is commonly used in the manufacture of wear plates, conveyor components, and pump liners. It is also used in the construction of heavy-duty machinery such as slurry pumps and mixing tanks.
3. Properties of Commonly Used Materials
Each of the materials used in the manufacture of mining wear parts has its unique properties that make it suitable for specific applications.
3.1 Manganese Steel
Manganese steel has excellent toughness and wear resistance, making it ideal for use in applications where heavy impact and abrasion are expected. This material is also capable of work-hardening, which means it becomes even harder and more wear-resistant with use.
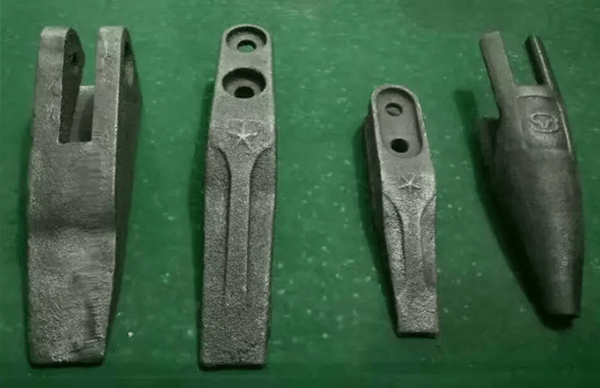
Figure 5: Manganese steel bucket teeth.
3.2 High Chrome Iron
High chrome iron is known for its high resistance to wear and corrosion. This material is also very hard, making it ideal for use in applications where heavy impact and abrasion are expected.
3.3 Tungsten Carbide
Tungsten carbide is known for its extreme hardness and wear resistance. This material is also very dense, making it ideal for use in applications where high impact and abrasion are expected.
3.4 Ceramic
Ceramic is known for its high resistance to wear and corrosion, as well as its ability to withstand harsh chemical environments. This material is also very hard and can withstand high temperatures, making it ideal for use in high-temperature applications.
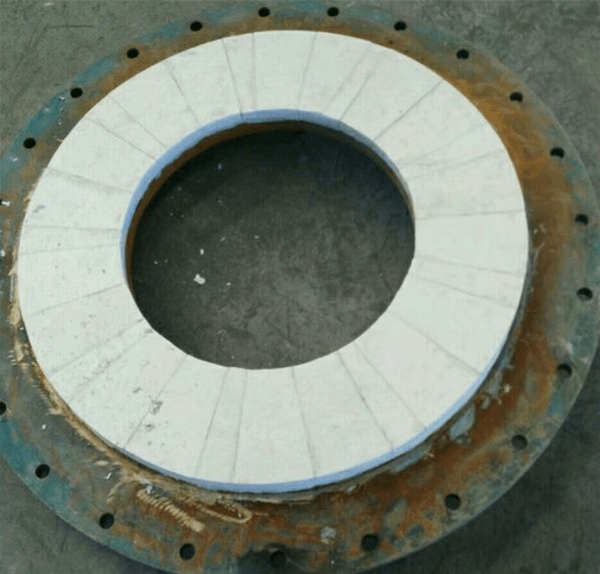
Figure 6: Cyclone ceramic liner.
4. Conclusion
In conclusion, mining wear parts are crucial components of any mining operation, and their proper maintenance and replacement are critical to ensuring the continued operation of mining equipment. The materials used in the manufacture of these parts are selected based on the specific application and requirements of the component being manufactured.
Manganese steel, high chrome iron, tungsten carbide, and ceramic are some of the most commonly used materials in the manufacture of mining wear parts. Each of these materials has its unique properties that make them suitable for specific applications.
Manganese steel is known for its excellent toughness and wear resistance, high chrome iron for its high resistance to wear and corrosion, tungsten carbide for its extreme hardness and wear resistance, and ceramic for its high resistance to wear and corrosion in harsh chemical environments.
By understanding the properties of these materials, mining companies can select the right material for the specific application, ensuring that their mining equipment operates optimally and efficiently.