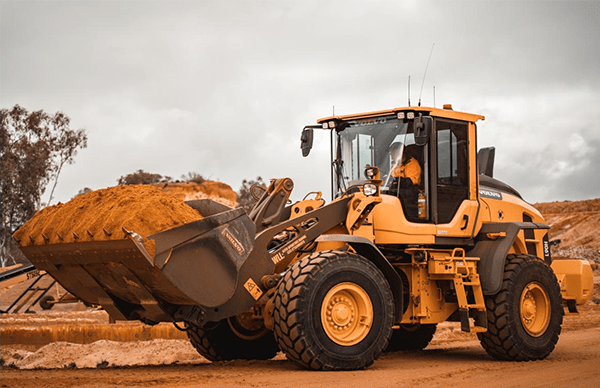
Figure 1: Loader.
Mining is a critical component of many industries, including construction, manufacturing, and energy. In order to extract minerals and other valuable resources from the earth, mining companies rely on a range of specialized equipment and machinery.
However, these machines are subject to significant wear and tear, particularly when used in challenging environments. To keep mining operations running smoothly, it is essential to have high-quality mining wear parts that can withstand the harsh conditions of mining sites.
In this article, we will discuss what mining wear parts are and the vital role they play in the mining industry.
1. What are Mining Wear Parts?
Mining wear parts refer to the components used in mining equipment that undergo significant wear and tear during operation. These parts include teeth, blades, buckets, and cutting edges, among others. Mining wear parts are made of high-quality materials such as manganese steel, tungsten carbide, and chrome iron, which are known for their durability and resistance to abrasion.
Mining wear parts are designed to withstand the harsh conditions prevalent in mining operations, including extreme temperatures, abrasive materials, and heavy loads. They are also subject to constant impact, pressure, and friction, making them vulnerable to wear and tear.
To ensure that mining equipment operates efficiently and safely, it is critical to use high-quality wear parts that can withstand these harsh conditions. Mining wear parts are used in a variety of mining applications, including drilling, crushing, grinding, and hauling.
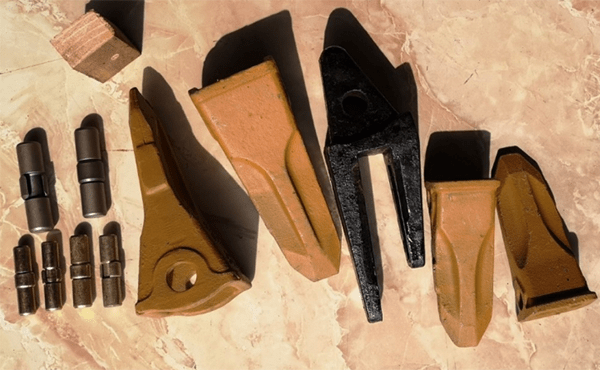
Figure 2: Bucket teeth and pins.
1.1 Common Mining Wear Parts
Some common mining wear parts include:
Crusher Wear Parts - These are used in crushers to crush rocks and other materials. Examples of crusher wear parts include jaw plates, mantle and bowl liners, and impact bars.
Grinding Mill Liners - These are used in grinding mills to protect the mill shell from wear and to improve grinding efficiency. Common types of grinding mill liners include lifter bars, shell plates, and end liners.
Haul Truck Wear Parts - These are used on haul trucks to protect them from wear and tear. Examples of haul truck wear parts include body liners, wear plates, etc.
Drill Bits - These are used in drilling equipment to cut through rock and other materials. Drill bits can be made from a variety of materials, including tungsten carbide, diamond, and steel.
Excavator Bucket Teeth: These are used in excavator buckets and are designed to break up and remove hard materials such as rock and ore. They are typically made from high-strength steel or tungsten carbide.
Dredging Pump Impellers: These are used in dredging pumps and are designed to withstand the abrasive and corrosive conditions of dredging. They are typically made from materials such as high chrome iron or rubber.
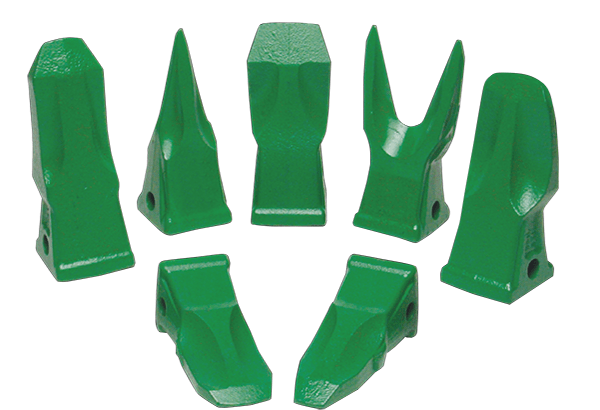
Figure 3: Different types of bucket teeth.
2. Role of Mining Wear Parts in the Mining Industry
The mining industry is a vital sector that contributes significantly to the world's economy. However, mining operations involve complex processes that require robust equipment and machinery. Mining wear parts play a critical role in ensuring that mining equipment operates efficiently and effectively, thereby enhancing productivity and profitability. The following are some of the key roles that mining wear parts play in the mining industry:
2.1 Protecting Equipment from Wear and Tear
Mining wear parts are designed to protect mining equipment from the wear and tear caused by abrasive materials such as rock, ore, and gravel. By protecting equipment from wear and tear, mining wear parts help to extend the life of equipment and reduce the need for costly repairs and replacements.
2.2 Enhancing Equipment Performance
Mining wear parts are designed to improve the performance of mining equipment. For instance, teeth and cutting edges are used in mining shovels to help them penetrate hard surfaces.
Similarly, bucket teeth are used in excavators to facilitate the digging process by providing better penetration and increased digging force. By improving equipment performance, mining wear parts help to increase productivity and reduce downtime.
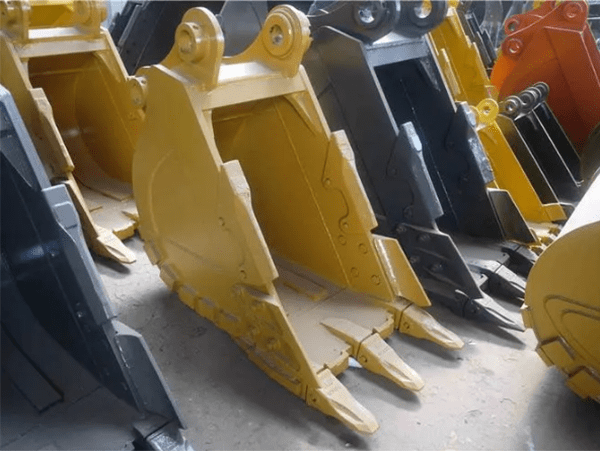
Figure 4: Buckets.
2.3 Reducing Maintenance Costs
Mining equipment is subject to significant wear and tear, which can lead to breakdowns and maintenance costs. Mining wear parts are designed to withstand the harsh conditions prevalent in mining operations, reducing the frequency of equipment breakdowns and maintenance costs. By reducing maintenance costs, mining wear parts help to improve profitability and productivity.
2.4 Improving Safety
Mining operations involve significant risks, including accidents, injuries, and fatalities. Mining wear parts play a crucial role in improving safety in the mining industry.
For instance, bucket teeth are designed to reduce the risk of material spillage, which can cause accidents. Similarly, cutting edges and blades are designed to prevent debris from flying off during excavation, reducing the risk of injuries.
2.5 Enhancing Efficiency
Mining wear parts are designed to enhance efficiency by reducing downtime and increasing productivity. For instance, bucket teeth are designed to provide better penetration, allowing for faster digging and increased productivity.
Similarly, cutting edges and blades are designed to improve the efficiency of excavation by reducing the need for rework. By enhancing efficiency, mining wear parts help to increase profitability and reduce operational costs.
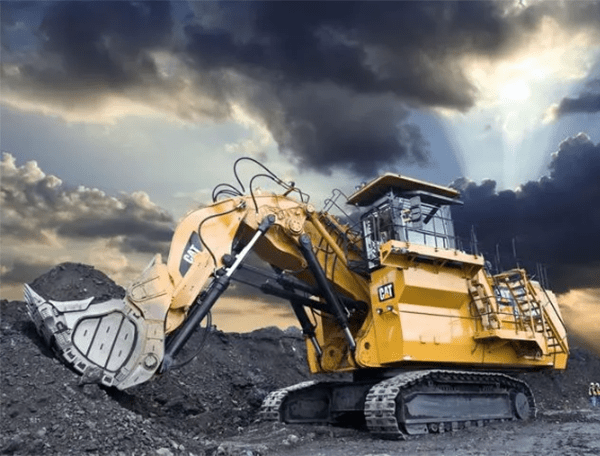
Figure 5: CAT front shovel excavator.
2.6 Lowering Maintenance Costs
Mining wear parts help to lower maintenance costs by reducing the need for frequent repairs and replacements. By using high-quality mining wear parts, mining companies can reduce the frequency of equipment breakdowns and the need for costly repairs.
3. Conclusion
In conclusion, mining wear parts are an essential component of the mining industry, playing a crucial role in ensuring that mining operations run smoothly and efficiently. These wear parts are designed to withstand the harsh conditions prevalent in mining operations, including extreme temperatures, abrasive materials, and heavy loads. They are also subject to constant impact, pressure, and friction, making them vulnerable to wear and tear.
To ensure that mining equipment operates efficiently and safely, it is critical to use high-quality wear parts that can withstand these harsh conditions. By using high-quality mining wear parts, mining companies can enhance equipment performance, reduce maintenance costs, improve safety, and enhance efficiency, thereby increasing profitability and productivity.