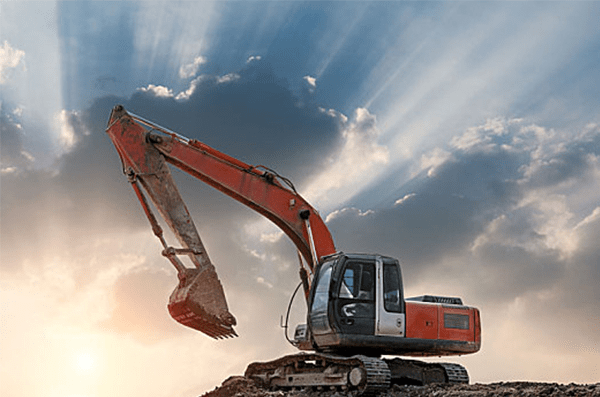
Figure 1: Excavator.
Wear parts are essential components of industrial machinery that are subject to regular wear and tear. They are designed to withstand the harsh conditions of various industrial processes, ensuring that machinery and equipment perform optimally.
Selecting the right wear parts for industrial applications is crucial to maintain the efficient operation of the machinery and minimize downtime. In this article, we will discuss the factors that should be considered when selecting wear parts for industrial applications.
Material Properties
The material properties of wear parts are critical to their performance and durability. Wear parts are exposed to high levels of stress, abrasion, and corrosion, which can cause premature failure if not properly selected. Therefore, it is crucial to choose materials that can withstand these conditions and ensure long-lasting performance.
There are several types of materials used to manufacture wear parts, including:
a) Steel: Steel is a common material used for wear parts due to its high strength, toughness, and durability. It is ideal for applications that involve heavy loads and high impact forces.
b) Ceramic: Ceramics are known for their excellent wear resistance, making them ideal for applications that involve abrasive materials. They are also resistant to corrosion and high temperatures, making them suitable for harsh environments.
c) Carbide: Carbide is a composite material made from tungsten or titanium carbide and a metallic binder. It is known for its excellent wear resistance and ability to withstand high temperatures and corrosion.
d) Polymer: Polymers are lightweight and offer excellent wear resistance. They are also resistant to corrosion and have low friction coefficients, making them ideal for applications that require high-speed operation.
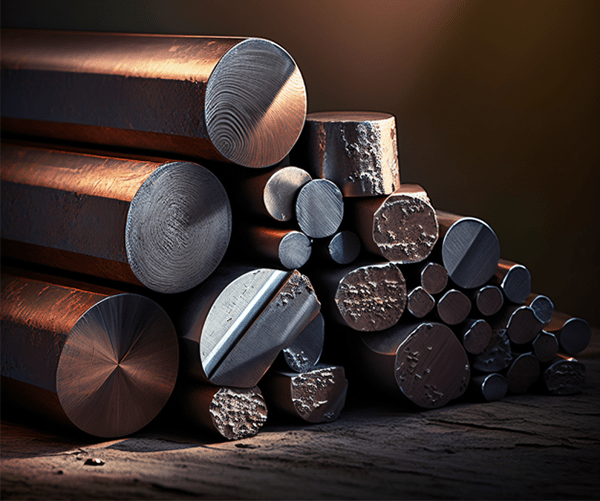
Figure 2: High manganese steel alloys.
When selecting wear parts, it is essential to consider the material properties of each type of material and how they align with the application's requirements. For example, if the application involves abrasive materials, ceramic wear parts would be the best choice due to their excellent wear resistance.
In addition, the material should be selected based on its compatibility with the other components of the machinery. Some materials may cause corrosion or damage to other components if they come into contact with each other. It is important to ensure that the wear parts are made of materials that are compatible with the other components of the machinery.
Application Requirements
The application requirements of wear parts are another critical factor to consider when selecting them for industrial applications. Wear parts must be designed to meet the specific needs of each application, ensuring optimal performance and longevity.
Some of the essential application requirements to consider include:
a) Load capacity: The load capacity of wear parts is crucial to their performance. They must be able to withstand the maximum load that they will be exposed to during operation.
b) Operating temperature: The operating temperature of wear parts is critical to their performance. They must be able to withstand high temperatures without degrading or losing their properties.
c) Speed: The speed of wear parts is essential to their performance. They must be able to operate at the required speed without causing excessive wear or damage.
d) Lubrication: Some wear parts require lubrication to reduce friction and prevent premature wear. It is essential to consider the lubrication requirements of each part when selecting them for industrial applications.
e) Corrosion resistance: Corrosion resistance is critical in harsh environments where wear parts are exposed to corrosive substances. It is essential to choose materials that are resistant to corrosion to ensure long-lasting performance.
f) Compatibility: Wear parts must be compatible with the machinery and equipment they are used on. It is crucial to ensure that the wear parts selected are compatible with the equipment's design and specifications.
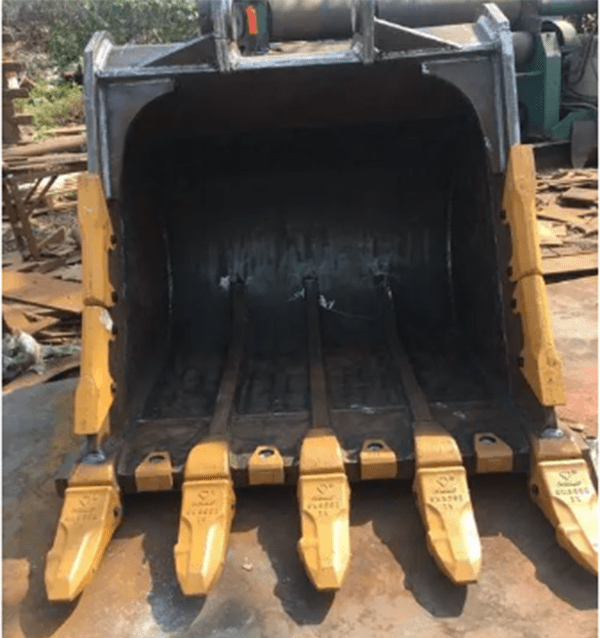
Figure 3: Excavator buckets wear protection parts.
Design
The design of wear parts is also an important factor to consider. The design should be optimized to minimize wear and tear and maximize the lifespan of the wear parts. The design should also be compatible with the other components of the machinery to ensure that it operates efficiently.
One design consideration is the shape of the wear part. The shape should be optimized to reduce friction and wear. A smooth surface and rounded edges can reduce the amount of friction and wear that occurs. Additionally, the design should ensure that the wear parts are easy to replace, so that maintenance can be performed quickly and easily.
Another design consideration is the thickness of the wear parts. Thicker wear parts may last longer, but they can also increase the weight and cost of the machinery. Thinner wear parts may be more affordable and lightweight, but they may need to be replaced more frequently. It is important to strike a balance between durability, weight, and cost when selecting wear parts.
Budget Constraints
Budget constraints are an important consideration when selecting wear parts for industrial applications. While it may be tempting to opt for cheaper alternatives, it is essential to consider the long-term cost implications of these decisions. Cheaper wear parts may save money in the short term, but they may not provide the necessary durability and performance required for the application.
When considering budget constraints, it is essential to evaluate the total cost of ownership of the wear parts. This includes the initial cost of purchasing the wear parts, as well as the cost of maintenance, repairs, and replacements over their lifespan. It is also essential to consider the impact of wear parts failure on production and downtime costs.
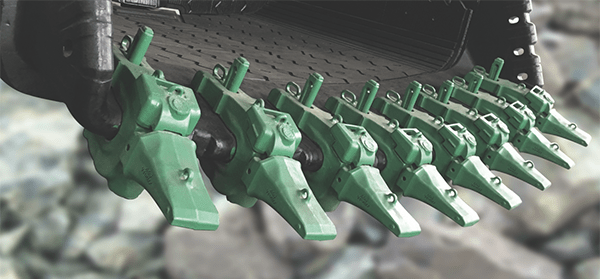
Figure 4: A&S custom bucket teeth.
Quality Assurance
Quality assurance is critical when selecting wear parts for industrial applications. Poor quality wear parts can lead to premature failure, resulting in costly downtime and lost productivity. Therefore, it is crucial to choose wear parts from reputable manufacturers who have a proven track record of producing high-quality products.
When selecting wear parts, it is essential to evaluate the manufacturer's quality control processes, testing procedures, and certifications. Manufacturers who have ISO certification or other quality assurance certifications are more likely to produce high-quality wear parts that meet industry standards.
Availability
The availability of wear parts is another important factor to consider. It is important to select wear parts that are readily available when replacements are needed. If wear parts are difficult to source or have long lead times, it can result in increased downtime and lost productivity.
When selecting wear parts, it is important to consider the supplier's availability and the lead time for replacements. It may be beneficial to select wear parts from a supplier that has a good track record for availability and reliability.
Conclusion
In conclusion, selecting the right wear parts for industrial applications is crucial to maintaining the efficient operation of machinery and minimizing downtime. The factors that should be considered when selecting wear parts include material selection, design, operating conditions, cost, and availability.
By carefully considering these factors, it is possible to select wear parts that are optimized for the specific application and that provide the best balance of durability, cost-effectiveness, and availability.