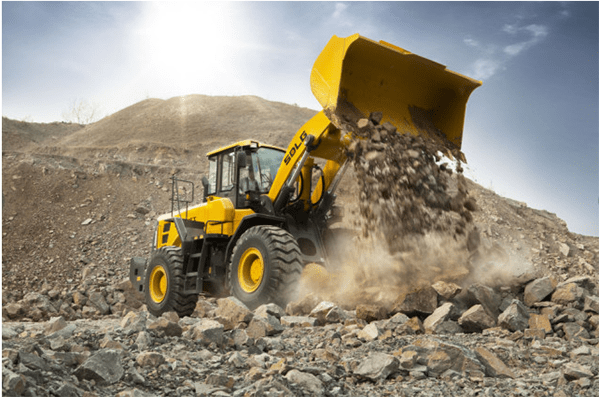
Figure 1: SDLG loader.
Mining and construction equipment are two of the most critical industries in the world, responsible for building and extracting the resources that our modern society relies on. These industries operate in some of the harshest environments, where machinery and equipment are subjected to constant wear and tear.
Wear-resistant parts are an essential component of mining and construction equipment. They are designed to withstand harsh working conditions, including abrasion, impact, and corrosion.
Wear-resistant parts play a critical role in ensuring that mining and construction equipment operates efficiently and effectively, reducing downtime and maintenance costs. In this article, we will discuss the benefits of using wear-resistant parts in mining and construction equipment.
Improved Equipment Lifespan
Mining and construction equipment are often subjected to harsh conditions such as abrasive materials, high pressure, and extreme temperatures. Without proper protection, the components of these machines would break down quickly, resulting in costly repairs and downtime.
Wear-resistant parts can help extend the lifespan of mining and construction equipment by protecting critical components from damage and reducing the need for frequent maintenance.
Components such as cutting edges, buckets, and bucket teeth that are made from wear-resistant materials can withstand the harsh conditions of mining and construction operations and maintain their shape and function for longer periods.
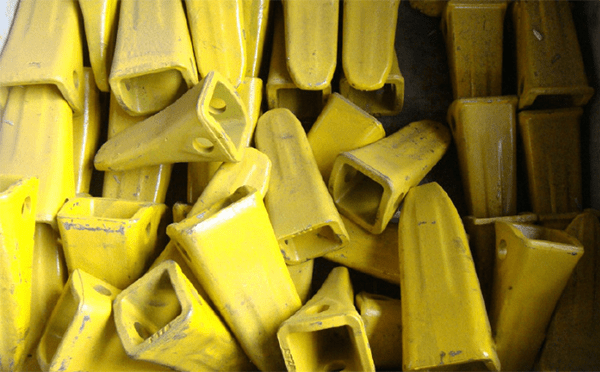
Figure 2: Bucket teeth.
Reduced Downtime and Maintenance Costs
Downtime and maintenance costs are two of the most significant expenses for any mining or construction company. When equipment breaks down, it can result in lost productivity, missed deadlines, and reduced profits.
Wear-resistant parts can help reduce downtime and maintenance costs by improving the longevity and reliability of mining and construction equipment. By using wear-resistant parts, companies can reduce the frequency of repairs and maintenance, allowing equipment to operate at maximum capacity for longer periods. This reduction in downtime and maintenance costs can lead to increased productivity and profitability for mining and construction companies.
Improved Safety
Mining and construction operations can be dangerous, with heavy machinery and equipment operating in close proximity to workers. Equipment failure due to worn-out components can lead to serious accidents and injuries.
Wear-resistant parts can help improve safety in mining and construction operations by reducing the risk of equipment failure. By using wear-resistant components, companies can ensure that their machinery and equipment operates efficiently and reliably, reducing the likelihood of accidents and injuries.
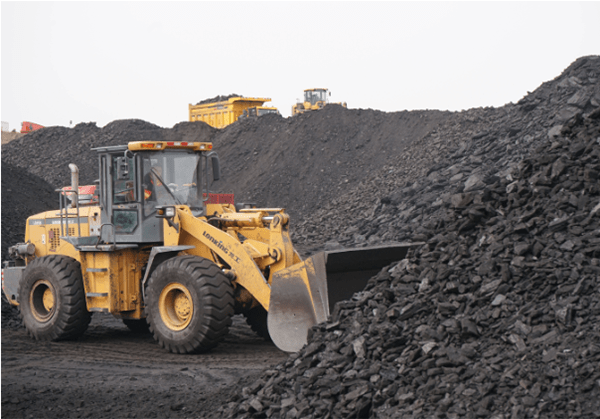
Figure 3: A loader at work.
Better Performance
Wear-resistant parts can also improve the performance of mining and construction equipment. For example, using wear-resistant cutting edges on buckets and blades can improve the efficiency of excavation and reduce fuel consumption. Similarly, using wear-resistant components in crushing and grinding equipment can increase the efficiency of ore processing and reduce energy consumption.
Wear-resistant parts can also improve the performance of equipment in extreme conditions. For example, using wear-resistant coatings on equipment exposed to high temperatures can prevent heat damage and maintain equipment performance.
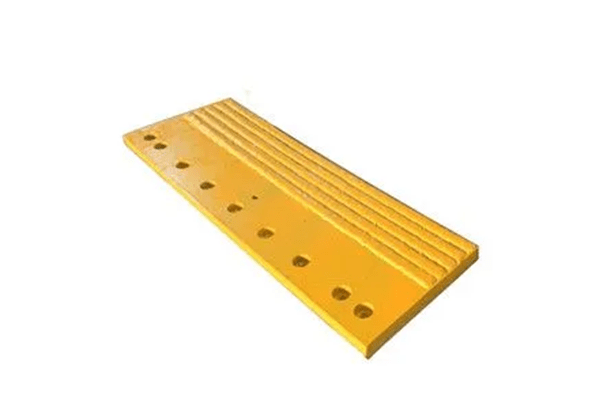
Figure 4: Bucket cutting edge.
Cost-effective
While wear-resistant parts may have a higher upfront cost than standard replacement parts, they can be a cost-effective solution in the long run. By extending the lifespan of mining and construction equipment and reducing the frequency of maintenance and repairs, wear-resistant parts can save companies money over time.
Furthermore, the improved performance and reliability of equipment resulting from the use of wear-resistant parts can lead to increased productivity and profitability, offsetting the initial cost of the parts.
Additionally, wear-resistant parts can help companies avoid the costs associated with equipment failure, such as lost productivity, missed deadlines, and worker injuries.
Improved Environmental Performance
Mining and construction operations have a significant impact on the environment. The use of wear-resistant parts can help to mitigate this impact by reducing the amount of waste generated from equipment maintenance and replacements. By extending the lifespan of equipment, wear-resistant parts reduce the need for frequent replacements, which can generate significant amounts of waste.
Additionally, wear-resistant parts can also improve the fuel efficiency of equipment by reducing the amount of energy required to operate it. This leads to reduced emissions and a lower carbon footprint for mining and construction operations.
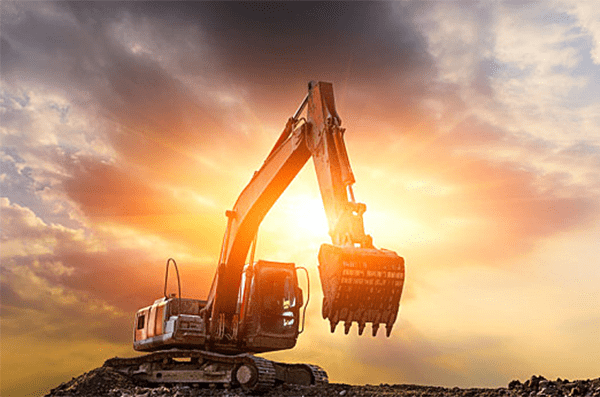
Figure 5: Excavator.
Enhanced Equipment Customization
Wear-resistant parts are available in a wide range of materials and designs, making it easy to customize equipment to meet specific operational needs. For example, some wear-resistant parts are designed to withstand extreme temperatures or corrosive environments, while others are optimized for high-impact applications.
By choosing the right wear-resistant parts, operators can optimize their equipment's performance and extend its lifespan.
Conclusion
In conclusion, the use of wear-resistant parts in mining and construction equipment offers numerous benefits, including improved equipment lifespan, reduced downtime and maintenance costs, improved safety, better performance, and cost-effectiveness.
By investing in wear-resistant parts, mining and construction companies can ensure that their machinery and equipment operates efficiently and effectively, reducing downtime and maintenance costs, as well as improving safety.
The selection of the appropriate wear-resistant part depends on the specific application and the type of wear and tear that the component is exposed to. Companies should work with knowledgeable suppliers to ensure that they are using the right type of wear-resistant part for their equipment.